Get This Report about Alcast Company
Get This Report about Alcast Company
Blog Article
Not known Incorrect Statements About Alcast Company
Table of ContentsThe Single Strategy To Use For Alcast CompanySome Ideas on Alcast Company You Should KnowAll About Alcast CompanyNot known Facts About Alcast CompanyThe Alcast Company StatementsThe Definitive Guide to Alcast Company
Chemical Comparison of Cast Aluminum Alloys Silicon promotes castability by reducing the alloy's melting temperature level and boosting fluidity during casting. Additionally, silicon adds to the alloy's toughness and put on resistance, making it beneficial in applications where durability is crucial, such as automotive components and engine parts.It additionally improves the machinability of the alloy, making it simpler to process right into ended up items. This way, iron contributes to the overall workability of light weight aluminum alloys. Copper increases electric conductivity, making it helpful in electrical applications. It also boosts deterioration resistance and contributes to the alloy's overall strength.
Manganese adds to the strength of light weight aluminum alloys and enhances workability (aluminum foundry). It is typically used in functioned aluminum items like sheets, extrusions, and profiles. The visibility of manganese help in the alloy's formability and resistance to cracking throughout fabrication procedures. Magnesium is a lightweight aspect that provides strength and influence resistance to aluminum alloys.
Alcast Company Things To Know Before You Buy
Zinc improves the castability of light weight aluminum alloys and assists manage the solidification process during casting. It improves the alloy's strength and solidity.
The main thermal conductivity, tensile stamina, yield stamina, and elongation differ. Among the above alloys, A356 has the highest thermal conductivity, and A380 and ADC12 have the most affordable.
Unknown Facts About Alcast Company
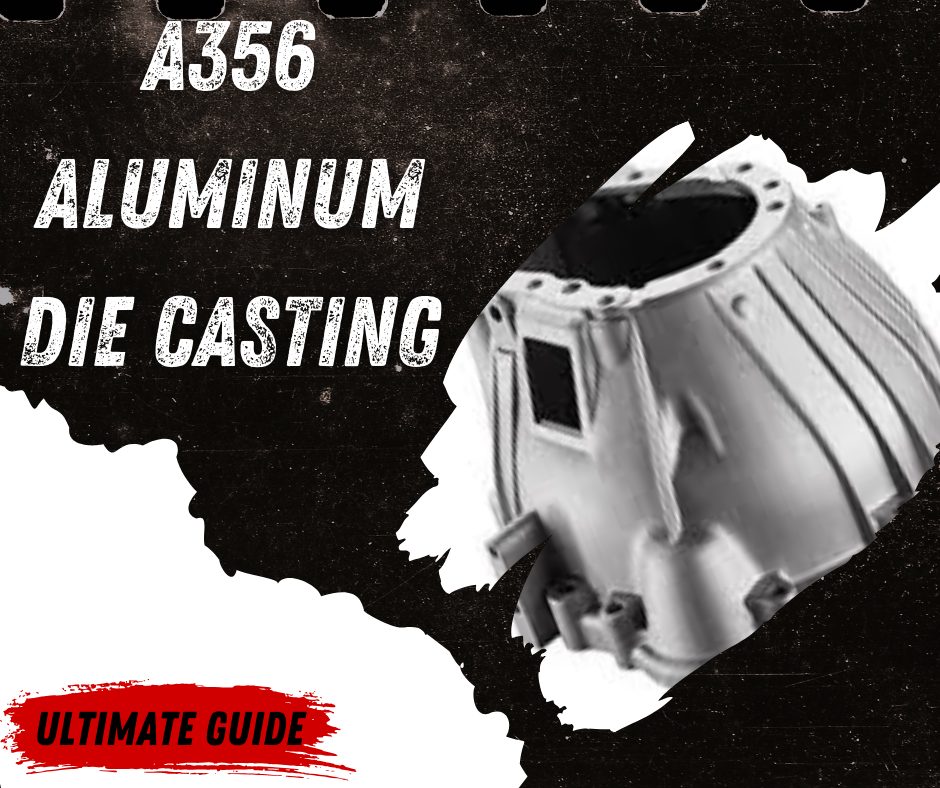
In accuracy casting, 6063 is appropriate for applications where detailed geometries and high-quality surface area coatings are critical. Examples include telecommunication enclosures, where the alloy's premium formability enables streamlined and visually pleasing layouts while keeping architectural integrity. In a similar way, in the Illumination Solutions market, precision-cast 6063 parts create classy and efficient lighting fixtures that need detailed forms and excellent thermal efficiency.
It brings about a better surface area coating and better rust resistance in A360. The A360 shows remarkable elongation, making it optimal for complex and thin-walled parts. In accuracy spreading applications, A360 is appropriate for markets such as Customer Electronics, Telecommunication, and Power Tools. Its boosted fluidity permits detailed, high-precision parts like mobile phone cases and communication gadget housings.
Alcast Company for Beginners
Its special homes make A360 a valuable option for accuracy spreading in these industries, improving item resilience and high quality. Aluminum alloy 380, or A380, is an extensively used spreading alloy this link with numerous distinct qualities. It uses superb castability, making it a suitable option for precision spreading. A380 shows excellent fluidity when molten, making sure detailed and detailed mold and mildews are accurately replicated.
In accuracy casting, light weight aluminum 413 radiates in the Customer Electronics and Power Tools sectors. This alloy's remarkable corrosion resistance makes it an excellent option for outside applications, making sure resilient, durable items in the discussed sectors.
Alcast Company for Beginners
As soon as you have made a decision that the light weight aluminum die casting procedure appropriates for your project, a crucial next step is determining on the most proper alloy. The light weight aluminum alloy you choose will significantly influence both the spreading process and the buildings of the final product. Since of this, you have to make your decision thoroughly and take an educated approach.
Determining the most suitable light weight aluminum alloy for your application will imply considering a vast variety of qualities. The first group addresses alloy attributes that impact the manufacturing procedure.
Rumored Buzz on Alcast Company
The alloy you choose for die spreading straight affects numerous aspects of the spreading procedure, like exactly how very easy the alloy is to work with and if it is vulnerable to casting defects. Warm cracking, likewise called solidification cracking, is a normal die spreading flaw for aluminum alloys that can lead to inner or surface-level tears or fractures.
Certain aluminum alloys are a lot more susceptible to hot splitting than others, and your option ought to consider this. One more usual defect found in the die casting of aluminum is die soldering, which is when the actors sticks to the die wall surfaces and makes ejection hard. It can damage both the cast and the die, so you must try to find alloys with high anti-soldering homes.
Rust resistance, which is already a significant feature of light weight aluminum, can differ substantially from alloy to alloy and is an important characteristic to think about depending upon the environmental conditions your product will be exposed to (Aluminum Castings). Use resistance is one more building generally looked for in light weight aluminum products and can differentiate some alloys
Report this page